Affordable, flexible system for off-line automated fettling and finishing
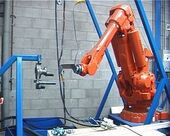
Period: 2002-2004
Funder: EU BRITE-EURAM Project No G1RD-CT2000-00445
Technical objectives:
- To develop flexible support and handling devices for castings up to 2.5 tonnes
- to develop and apply robust sensing technology for part recognition, part location and process control, and to devise closed loop control systems
- to create process models to support off-line programming and
- to optimise process efficiency to develop new methods, software and tool movement strategies for the off-line programming of the robot path.
The project advanced the technology beyond the state-of-the-art by developing and proving an off-line programmable autonomous system capable of carrying out a combination of fettling and finishing operations with accurate control on medium/large castings. The main project output was a proven prototype cell that was exploited after completion of the project, and resulted in the development of the ABB force control products.
Url: http://www.robot.lth.se/proj/autofett/
Partners: TI (Project Co-ordinator), UK; The Katholieke Universiteit Leuven (KU Leuven), B; Lips/Wärtsilä , propeller manufacturer, NL; Aceros del Ebro - steel foundry, E; Cometna - steel foundry, P; Kranendonk - robotic system integrator, NL; ABB - robotics manufacturer, S; CR-FIAT - Fiat research consortuim, I.
ULUND/LTH was included as a subcontractor for development of the force/torque-control together with ABB.